Case Studies
B&Q Distribution Centre, Worksop
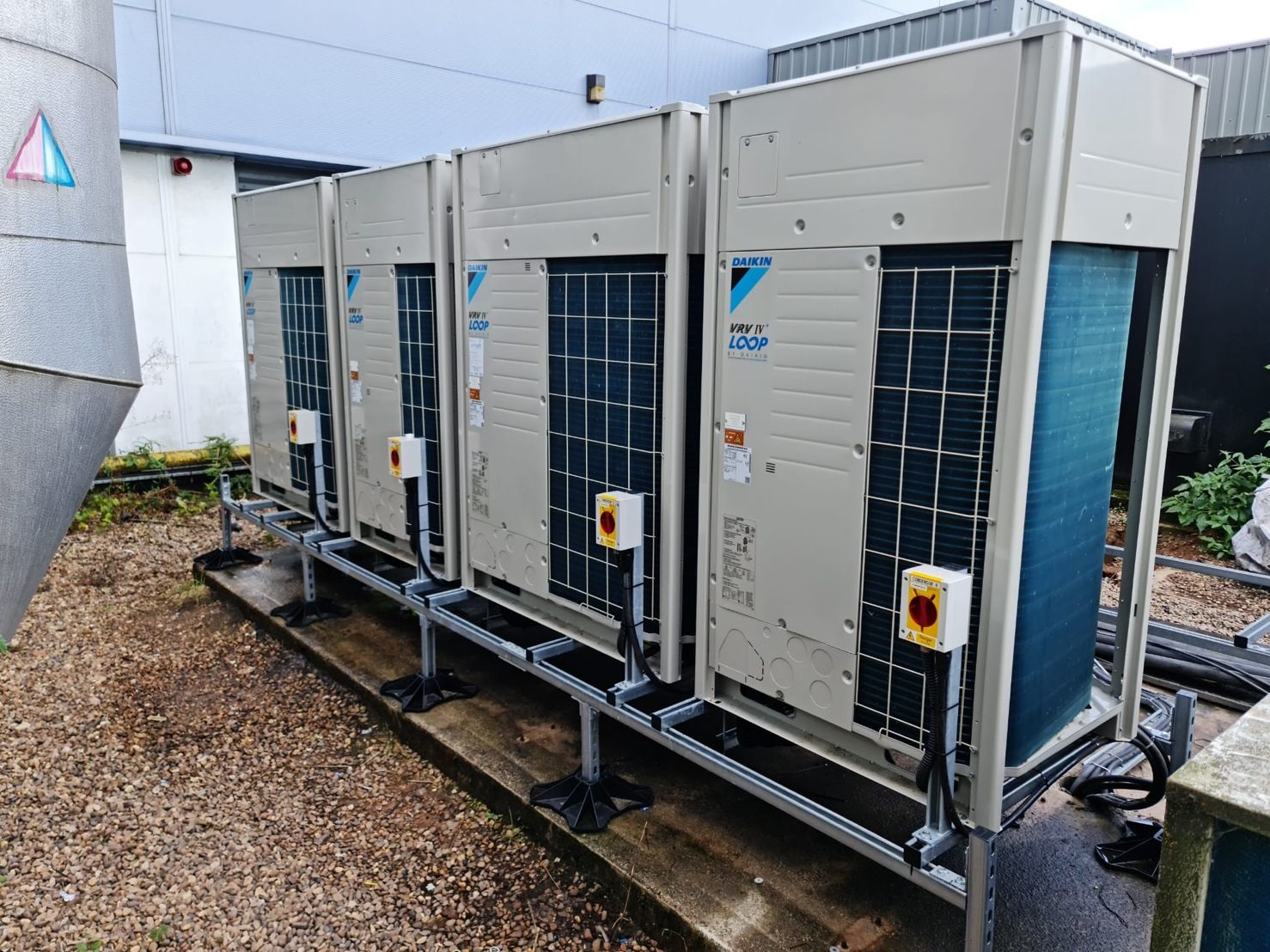
As a Daikin D1+ dealer & installer, Airmaster Air Conditioning Ltd along with several other local D1+ rated companies were invited to tender for the large Air Conditioning replacement project at the B&Q Distribution Centre in Worksop.
We were asked to present 2 tender applications, the first to carry out a full like-for-like AC replacement of the existing 15 year old Sanyo systems, the second was to put forward our own design & build application.
The Airmaster Contracts team presented a perfect tender application which included a full Hevacomp thermal imaging building report, giving us the precise up to date technology to supply the correct AC equipment in the right areas, this was carried out by our in house Design team at Airmaster Air Conditioning Ltd.
The project included; the full removal of the existing AC systems, with full replacement of 6 large Daikin Europe VRF systems, 2 Comms room double split systems, the project also included the Daikin ‘reclaim with confidence’ and ‘commission with confidence’ package. This was finished with a full mains electrical upgrade to all internal and external AC systems.
This was carried out on a very tight 8 week timeframe, along with all buildings still in full use and strict Covid restrictions earlier this year, the Airmaster Air Conditioning Ltd team pulled out all the stops to complete a fantastic project on time.
The B&Q Worksop Engineering & Facilities Manager Dave Horton and his team were brilliant to work with and had nothing but praise for the Airmaster installation Engineers.
To download a PDF of the case study please click here.
Paul Wilkins, Corporate Clients Division Manager at Daikin
“Well done to everyone involved at Airmaster Air Conditioning Ltd. Your tender submission was spot on, fulfilling the brief perfectly and then going beyond it too. The project ran like clockwork thanks to your professionalism. The client understood the long-term importance of marrying a high-quality installation with high quality equipment. A great project.”
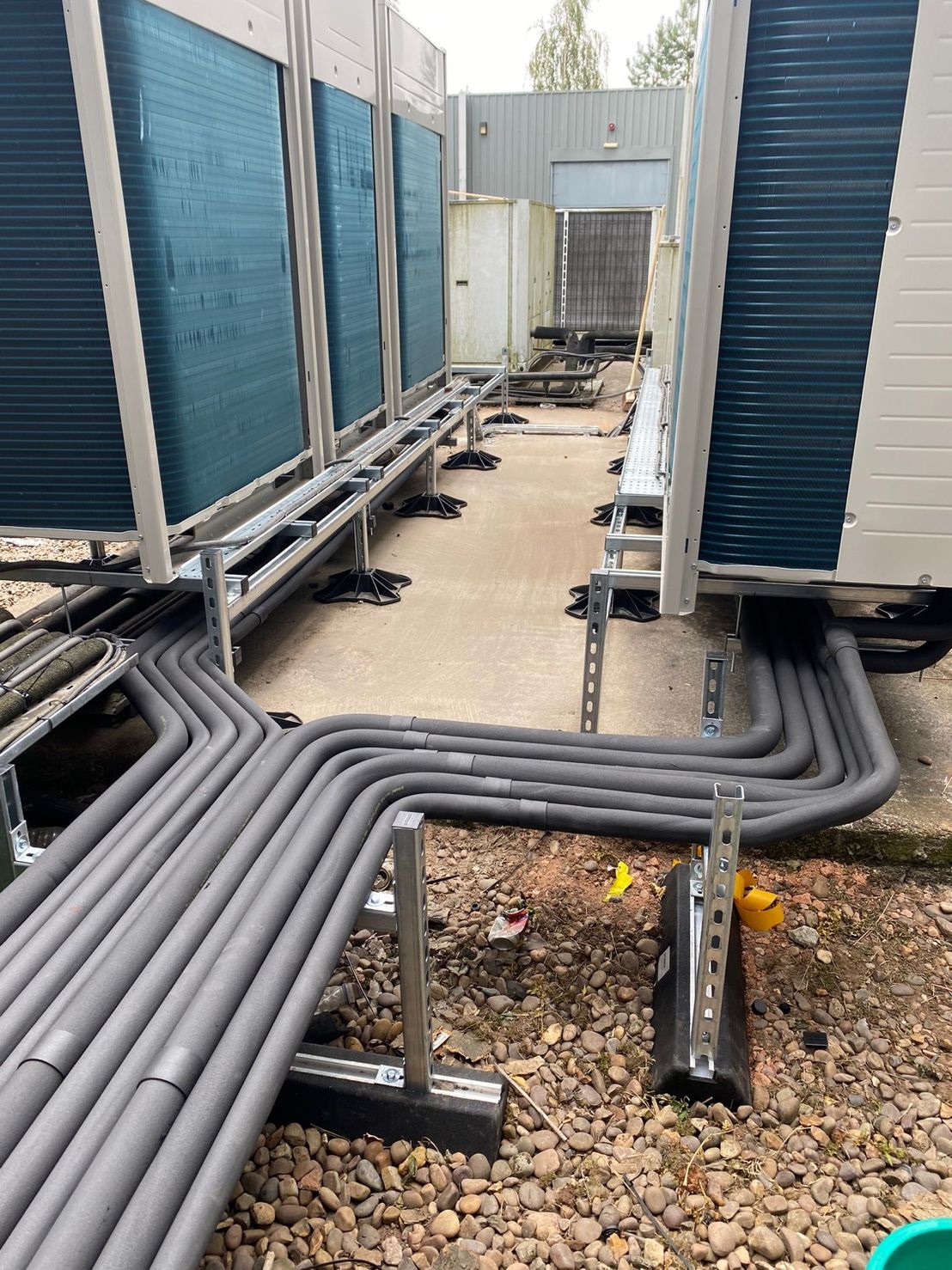
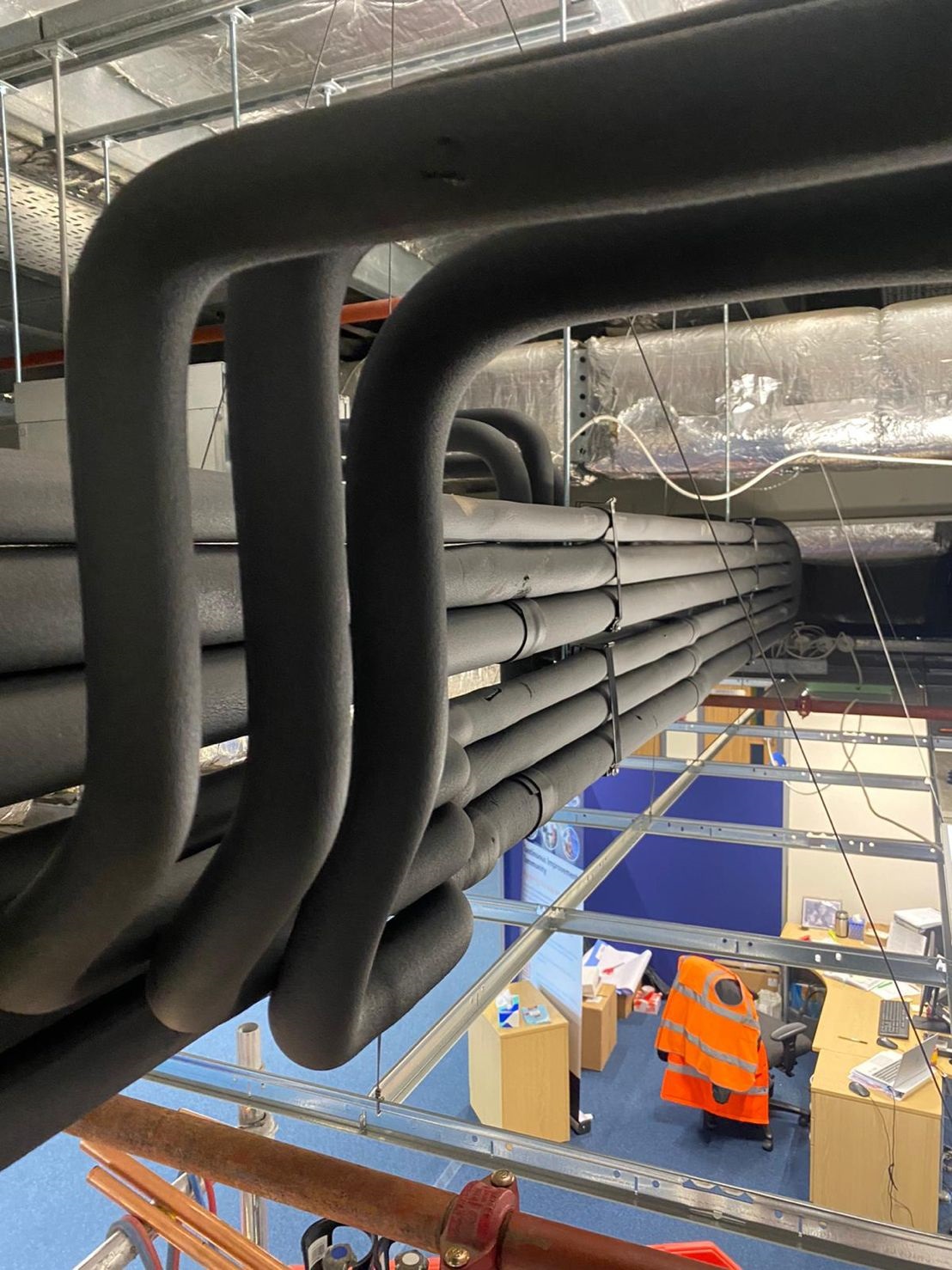
Cold room supply and install - Doncaster
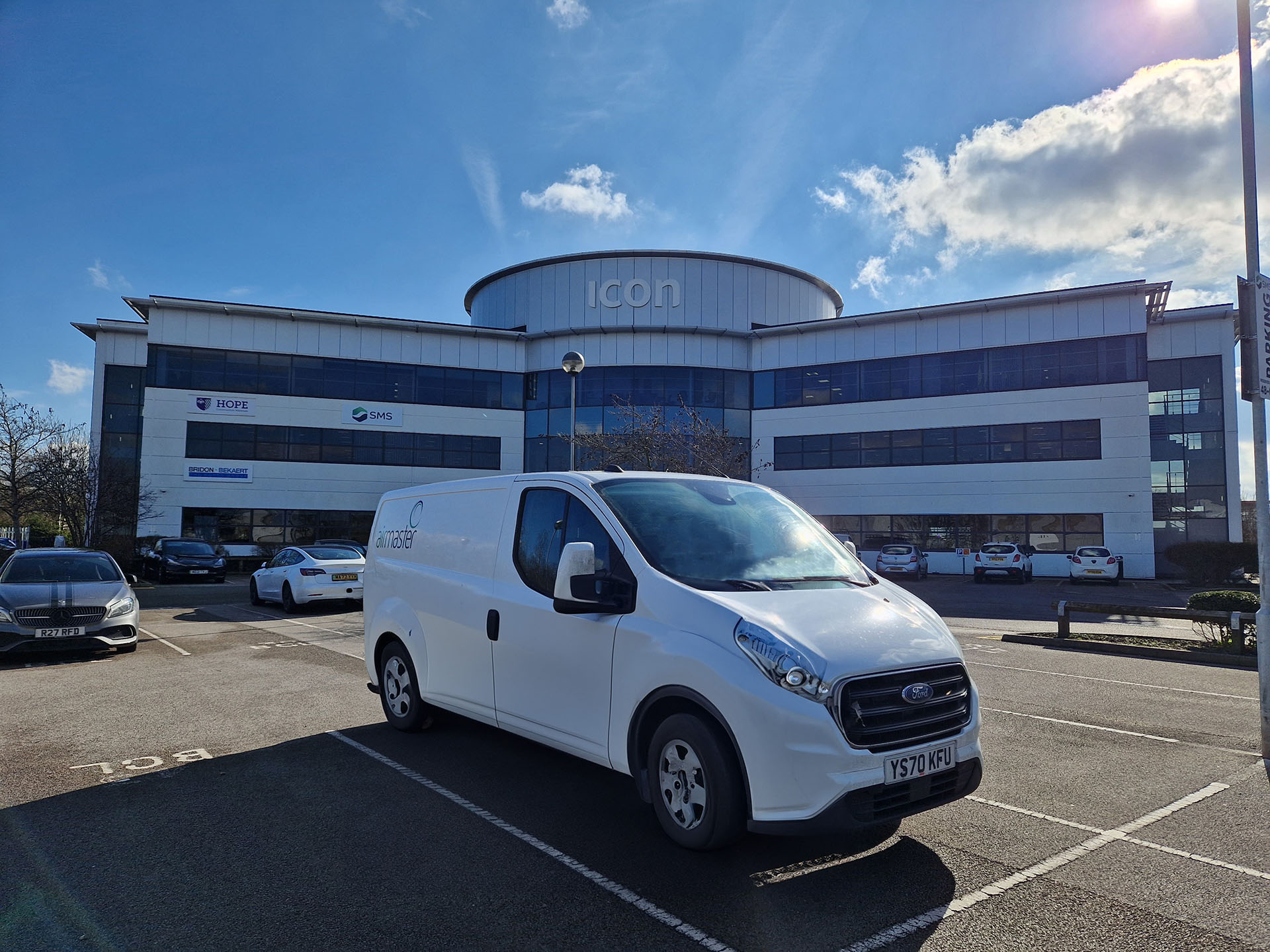
Airmaster have completed the supply and install of a cold room for Highfield Coffee Social in Doncaster as part of their fit out of their new coffee shop.
Main Contractor: Togel Contractors
Project Manager: Stephanie Lagan–Collins, Fatfish Design
Airmaster supplied and installed the walk-in chiller cold room, refrigeration equipment, cold room shelving and a personnel entrapment alarm.
We also supplied and installed a stainless-steel kitchen canopy with integrated supply and extract, along with stainless steel wall cladding.
The existing A/C fan coil units were relocated, and we supplied and installed additional heat recovery units, along with upgrading all the ceiling grilles to matte black to fit with the new interior decor of the public facing coffee shop space.
To download a full copy of our case study please click here
“We have worked with Airmaster for around 20 years for all our air conditioning requirements throughout our business sites in Doncaster, including PPM, servicing, server room design and install when relocating offices.
When we have had problems arise in the past, all it has taken is a phone call to Airmaster, and on many occasions they have gone the extra mile to help us resolve the issue quickly and efficiently.
So, when we began to develop plans for Highfield Coffee Social, we knew we were in capable hands with the team to fulfil our specific requirements. The whole process, from initial plans through to fit and commission, was faultless, and we are delighted with the outcome.”
Mike Stark, Facilities Manager, Highfield
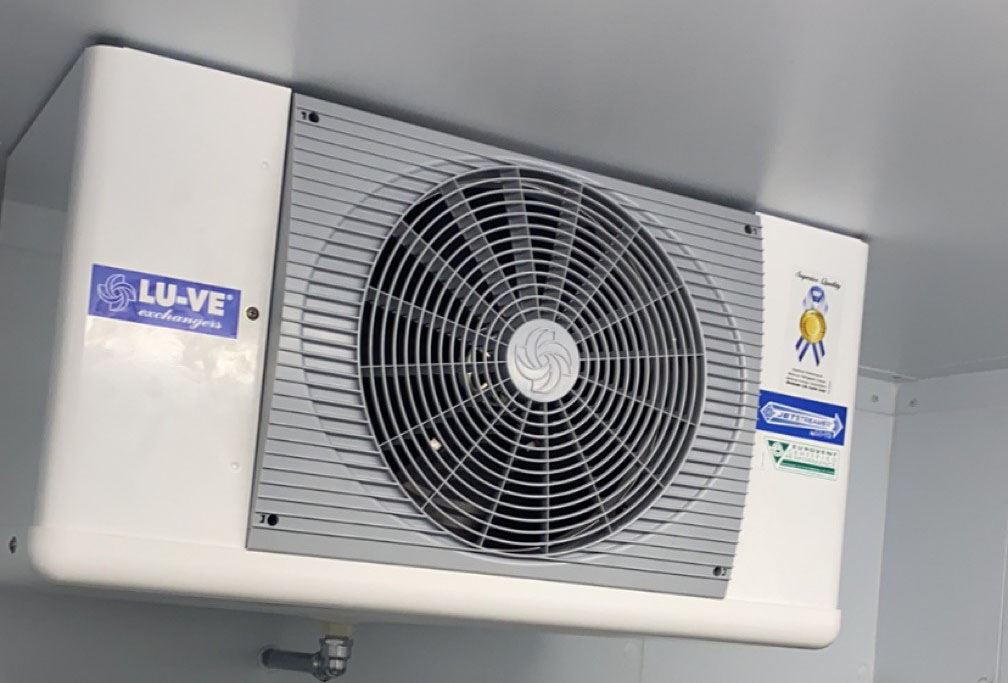
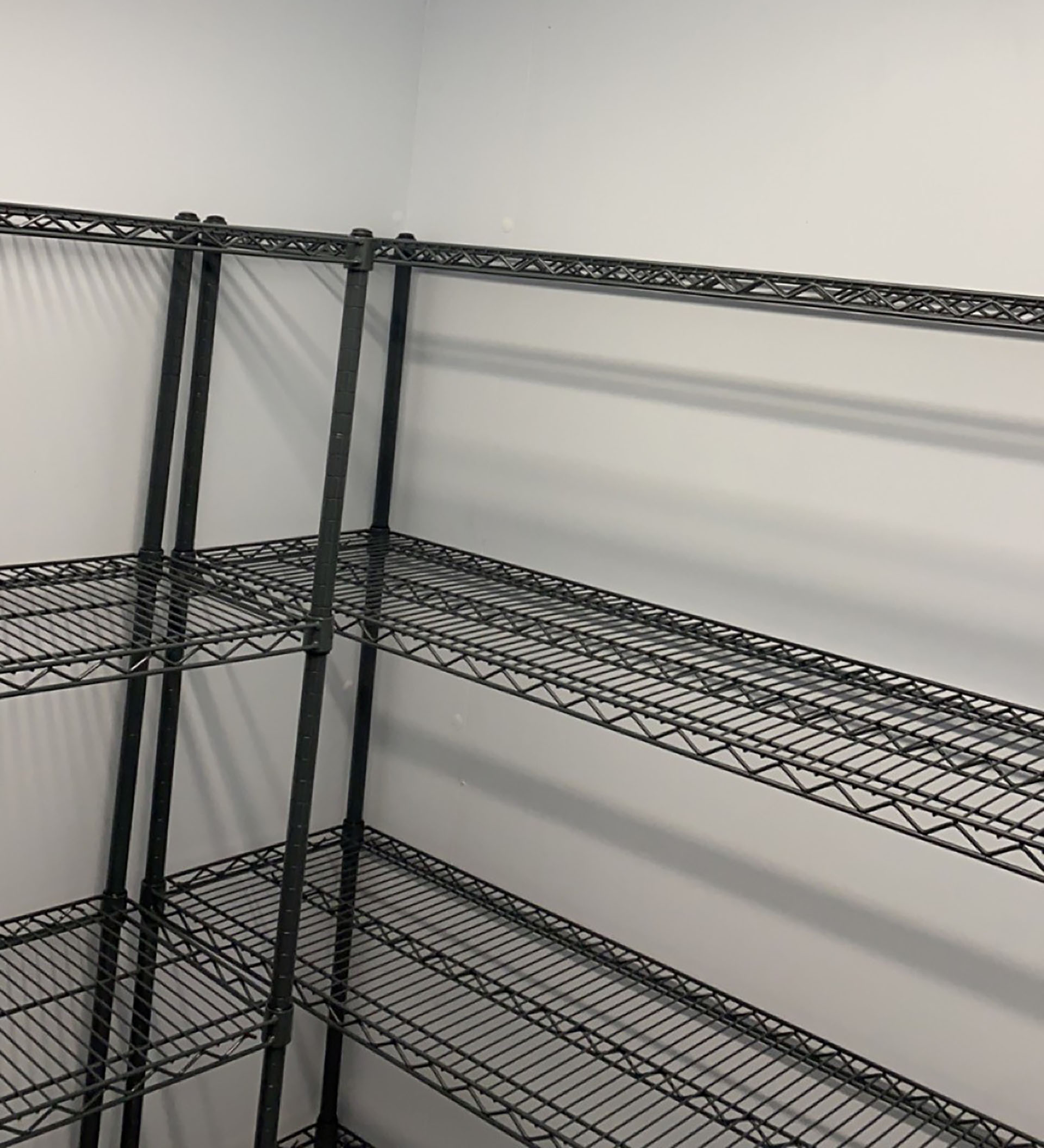
AESSEAL, global manufacturing headquarters, office fit out, Rotherham
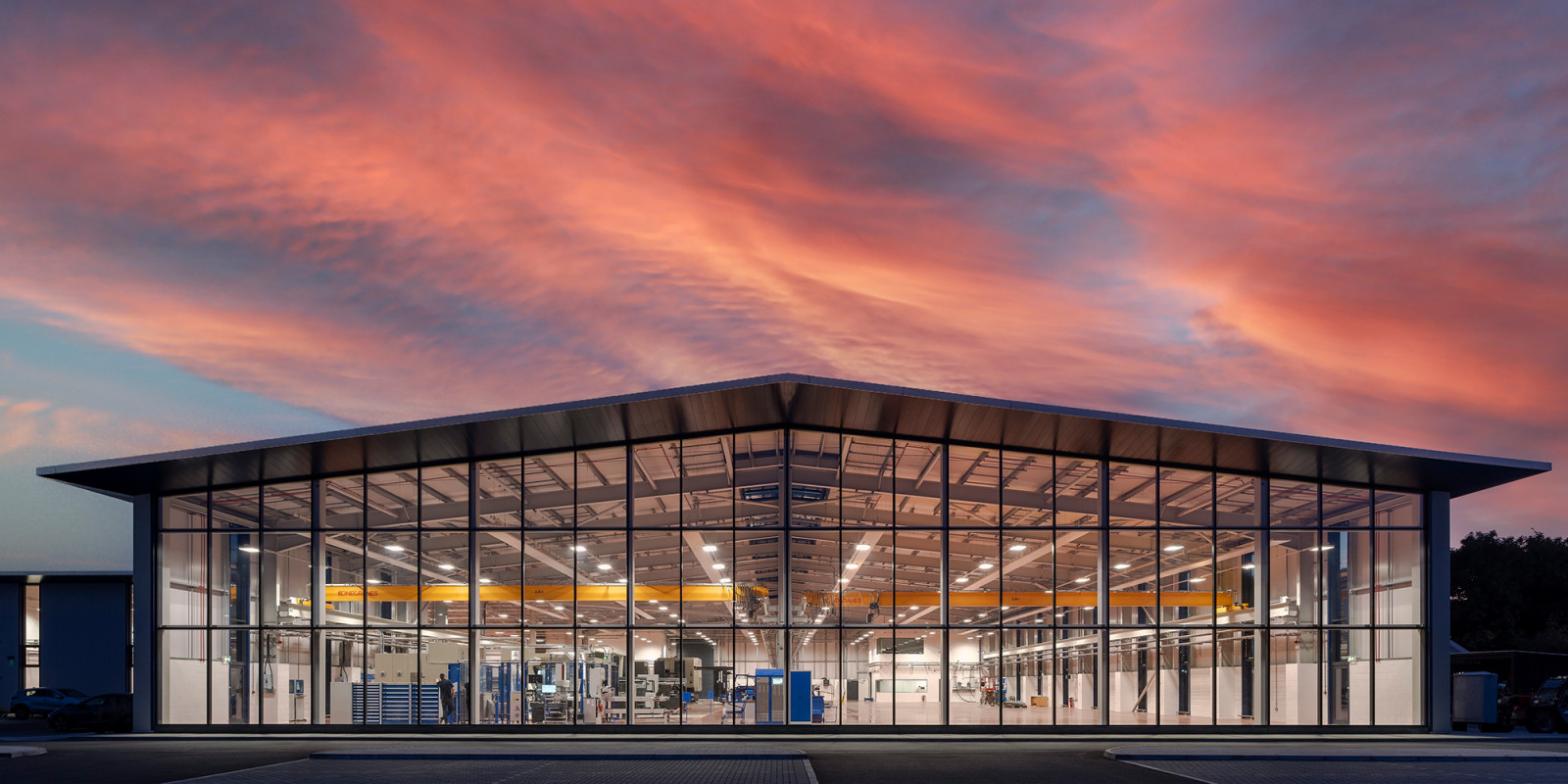
Sector: Office fit out
Contract: Mechanical install
Airmaster installed a new high efficiency Mitsubishi Hybrid system to the new modernised office space at AESSEAL, whose global headquarters are based in Rotherham, South Yorkshire.
Over the years regulations are ever-changing to lower the impact of air conditioning refrigerants on the environment and reduce global warming. The team at AESSEAL tasked Airmaster to provide them with sustainable air conditioning systems which target both their energy efficiency conscious operations and further reduces their impact on global warming. The system will also ensure the internal office environment is adaptable to the constant climate changes.
The project installation was for a highly energy-efficient Mitsubishi Electric R32 Hybrid HVRF system which has a lower global warming potential (GWP) of 675 over its R410a VRF predecessor in 2018. This system also utilises a hybrid between refrigerant and hydraulic water to provide simultaneous heating and cooling to the office space, further reducing the GWP potential.
Primary ductwork modifications were carried out to deliver fresh air to the void-mounted fan coil units which precondition fresh air prior to distribution into the office space. Then new secondary ductwork which was connected, thermally insulated, and balanced onto linear grilles was installed the full length of the office space. Hybrid systems utilise part refrigerant / part hydraulic water, therefore requiring a category 5 break tank, PRV, pressure monitoring and distribution pipe work to the HVRF selector box for filling of the hydraulic water circuits of the system.
The system is controlled via a central touch screen intelligent controller, allowing multi functional zoning, time control and system diagnostics, along with integration to the building’s automatic BMS controls system using BACnet protocol.
This project was completed in August 2024, with the second phase of the project commencing in February 2025 in another part of the large AESSEAL Rotherham facilities. This will be followed by additional works later in the year to de-carbonise the building further by removing the existing gas boilers and installing more energy efficient systems utilising similar technology as their warehouse heating. It’s been great to work alongside such a forward-thinking company who share our desire to move towards systems with higher efficiency and lower GWP potential.
To download the PDF of the case study please click here
“The installation of the first-floor hybrid system was completed with the upmost professionalism, integrity and care. The support from Airmaster in the office was outstanding along with the support the engineers showed, which was brilliant. The lead time from placing the order to the kit arriving and being installed was a really good turnaround. I have had feedback from those within that office saying how grateful they are of the upgrade and can tell the difference with the new system.”
Billie Clark
Facilities Maintenance & Project Co-Ordinator, AESSEAL
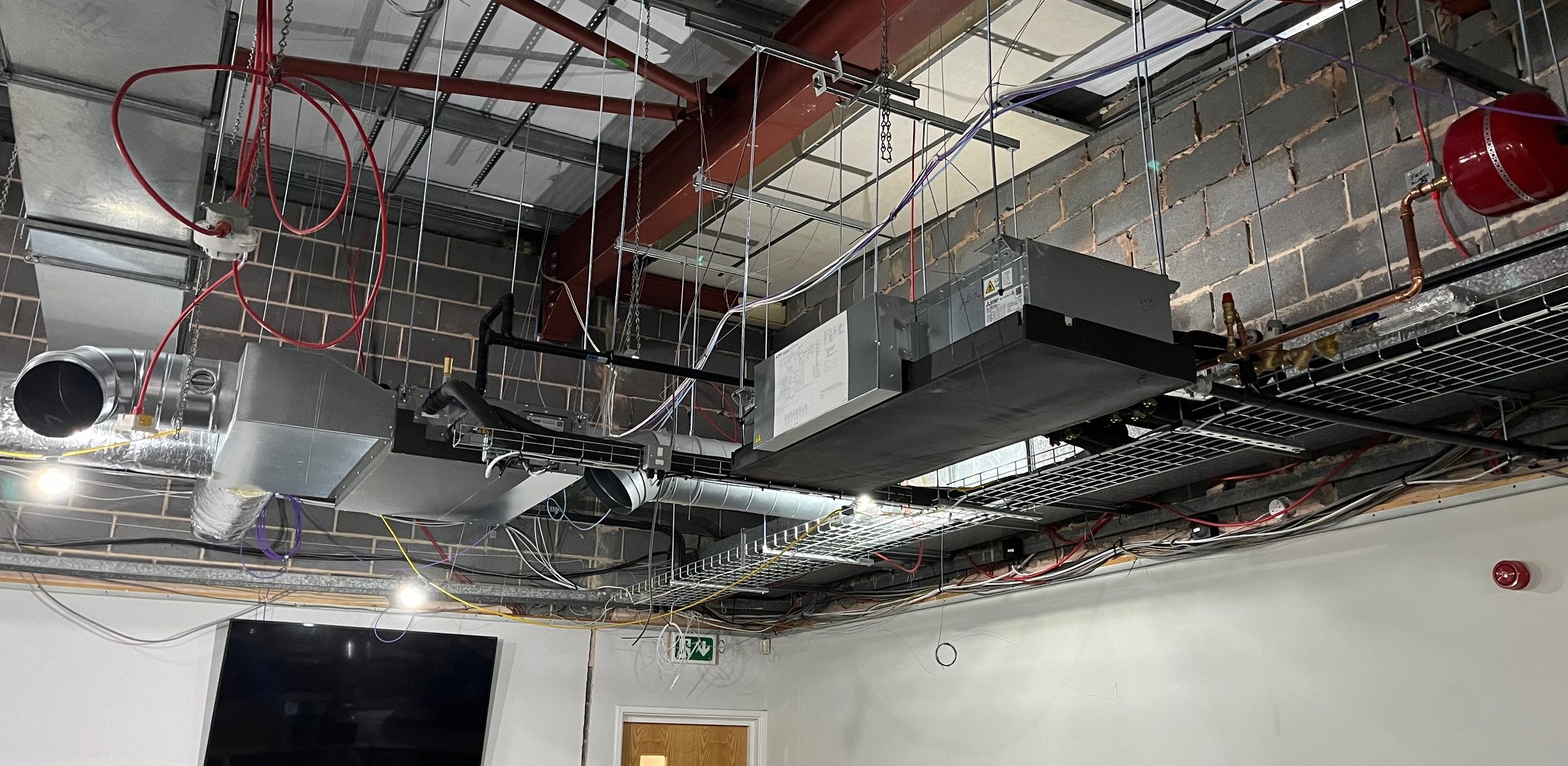
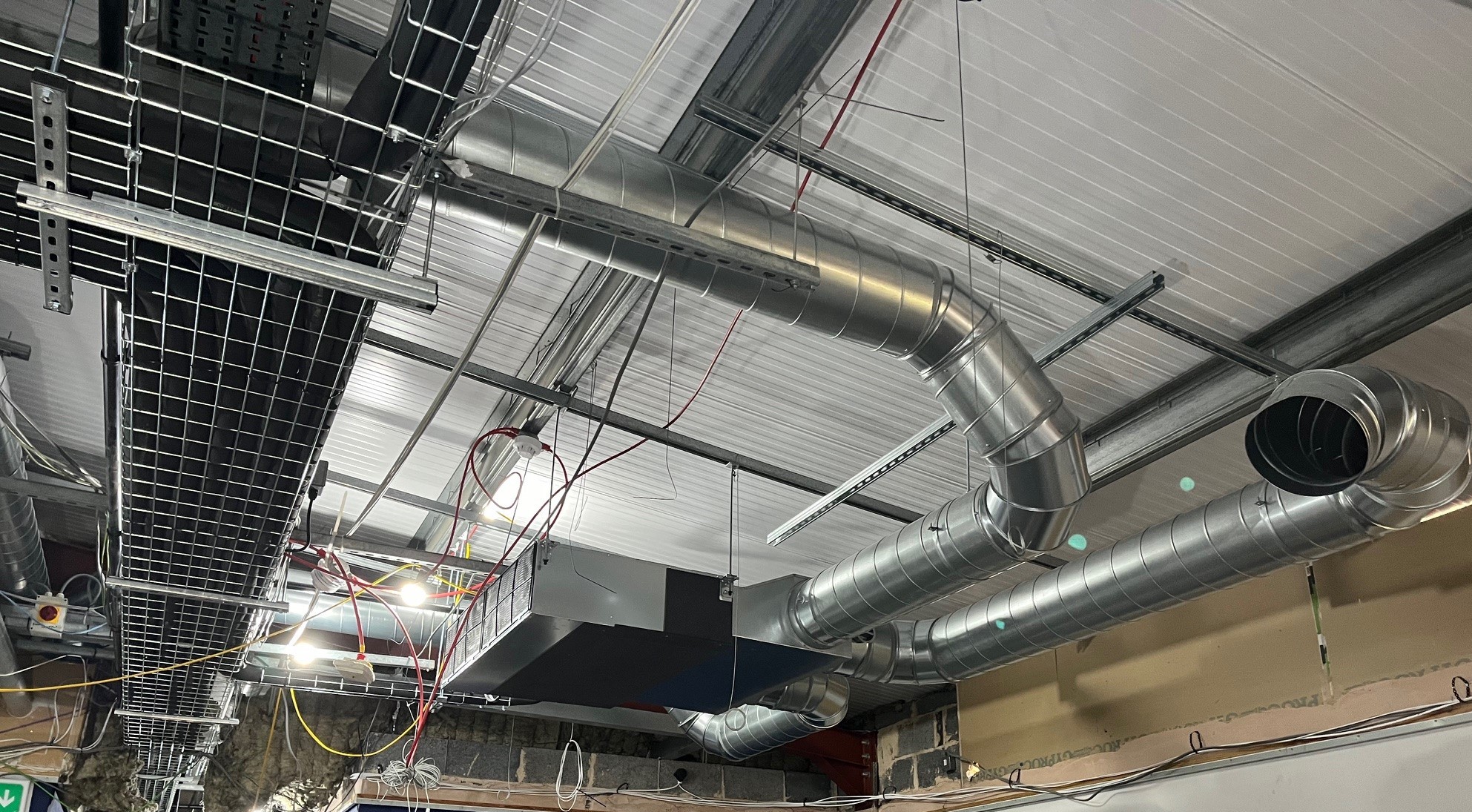
Business Park Offices
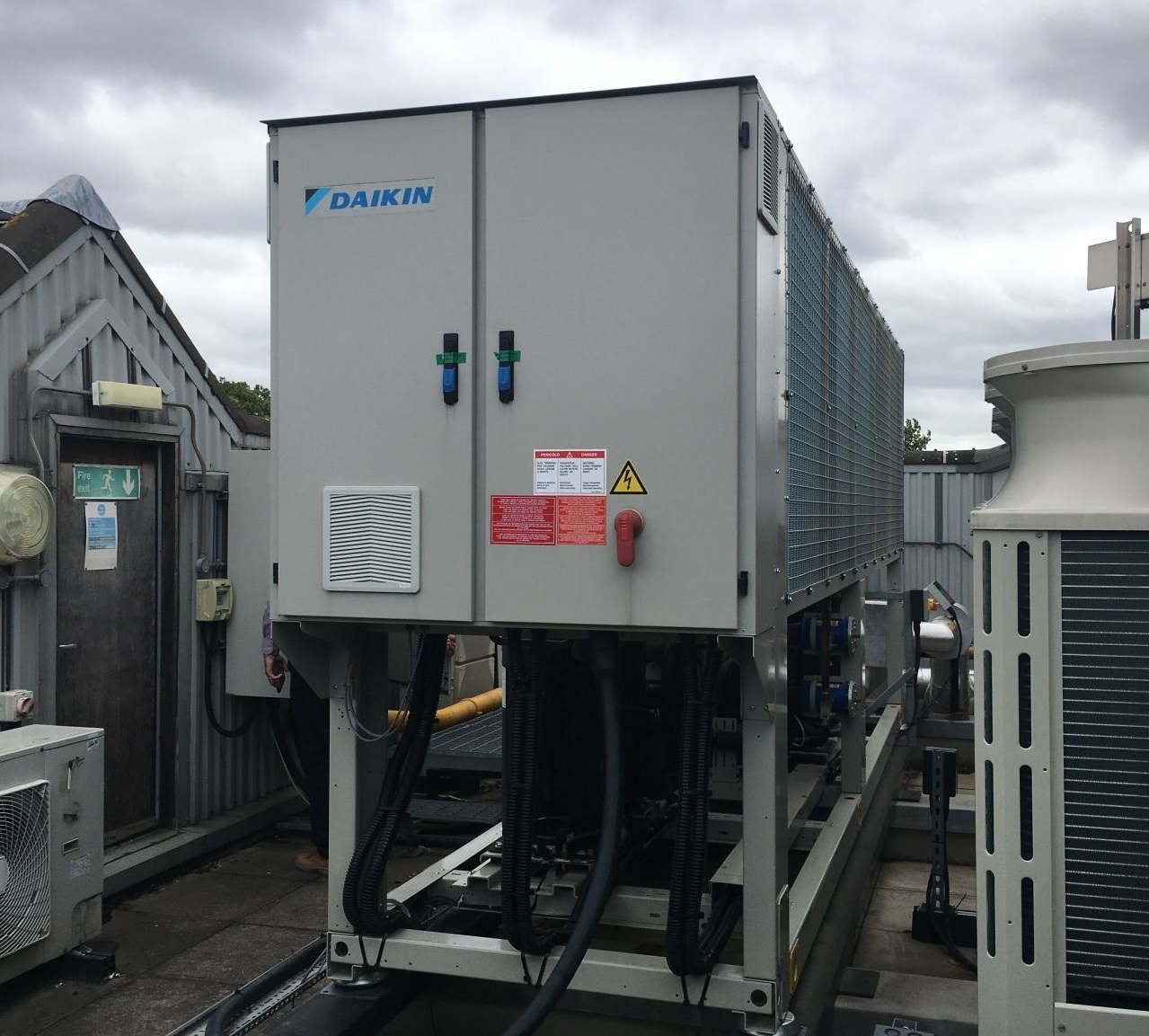
The photos below are from whilst we were completing a mechanical fit in Watford. The landlord owned various buildings on the business park and there was a relatively new Daikin chiller on the roof that was surplus to requirements due to the whole building converting to VRF/V.
There was however another chiller at the end of its life on another building so whilst in contract and to make space for our new condenser banks we successfully disconnected both chillers, controls power and water, craned the old one off to be disposed, then the new one off one building, re set up the crane location to lift it onto the other building in the same day.
Then the week that followed, re piped, dosed, insulation and cladding, power, BMS, water balancing and commissioning. Needless to say good planning, preparation and communication meant this all went smoothly and we envisage for every project.
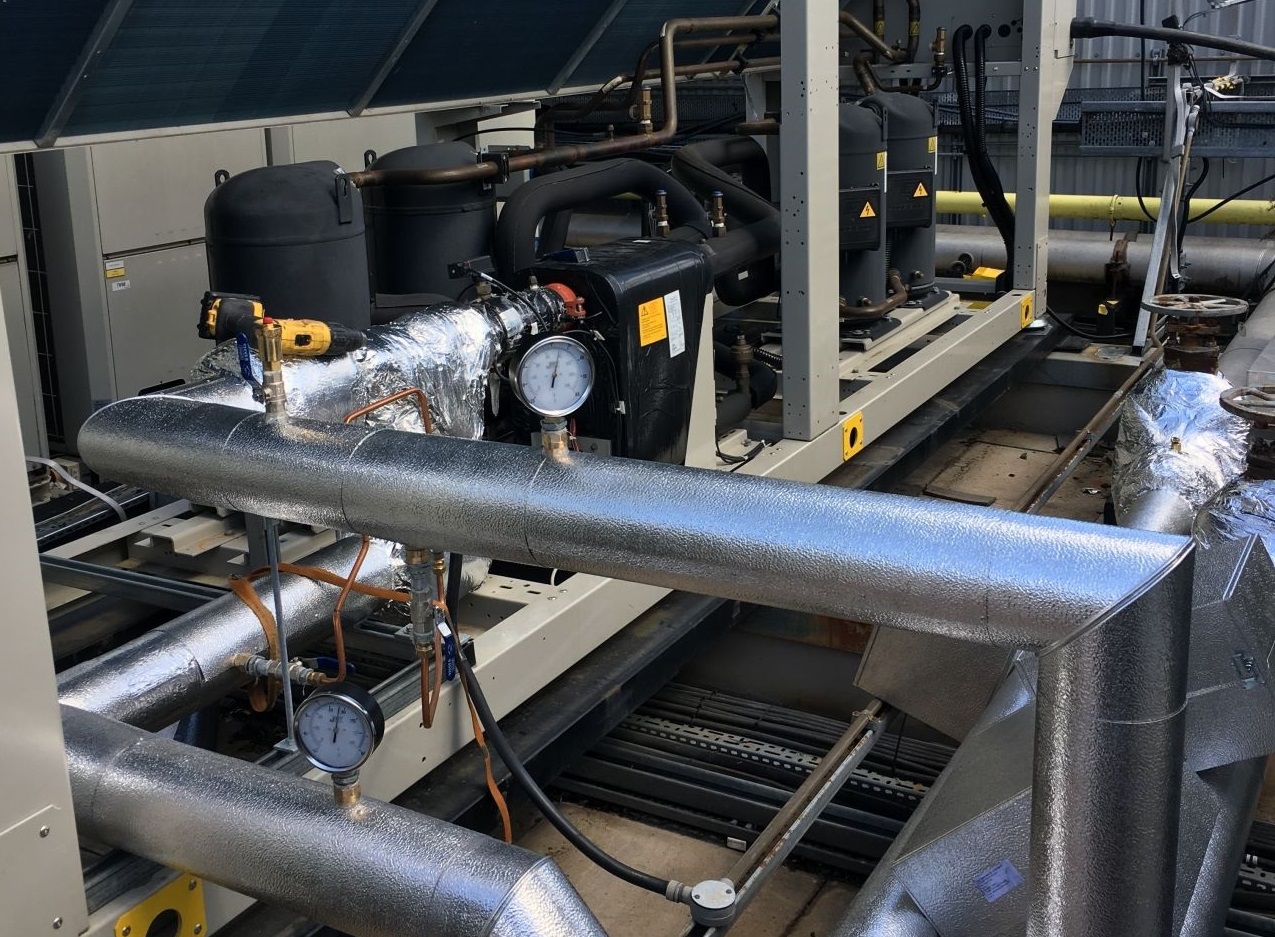
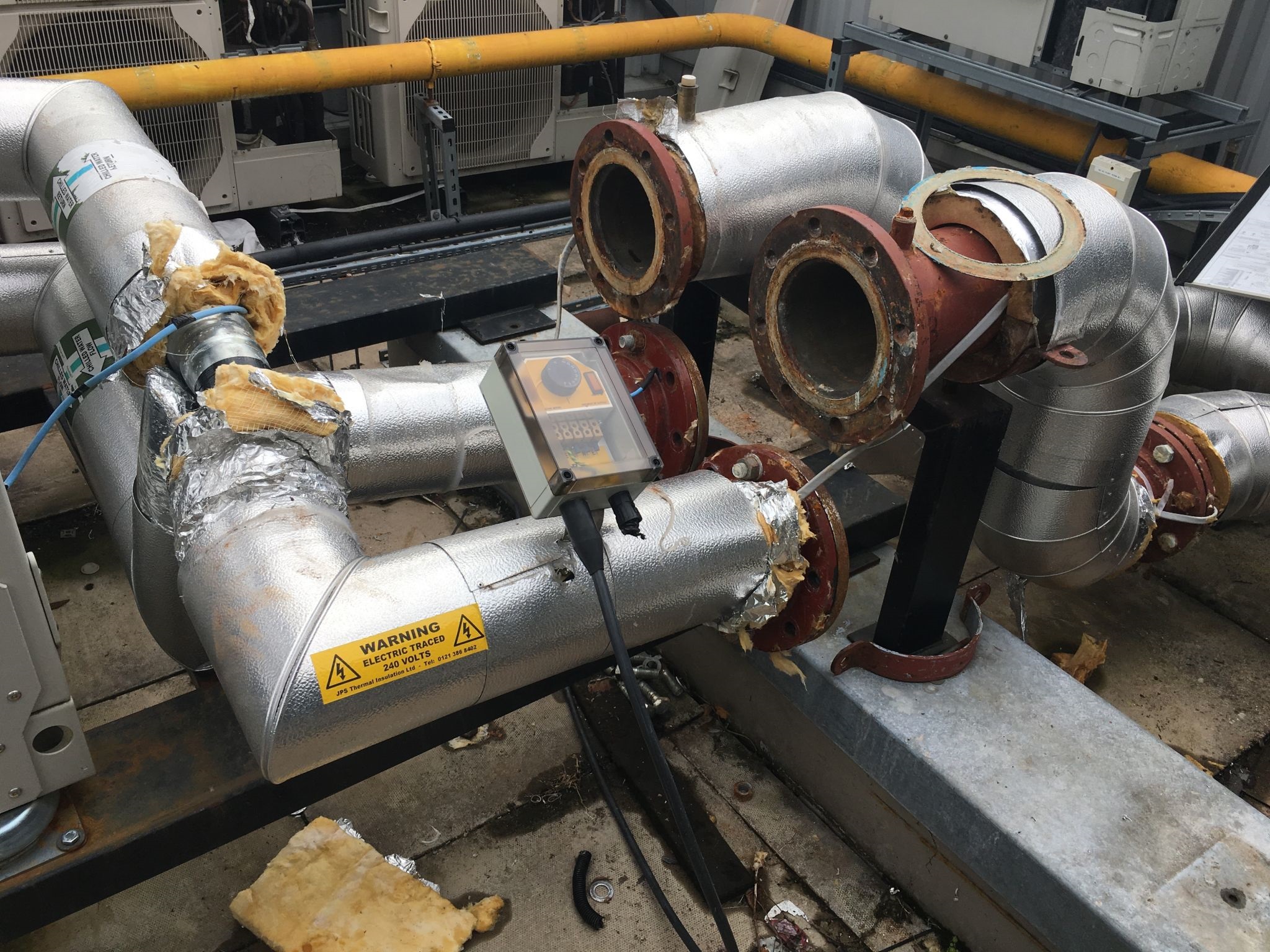